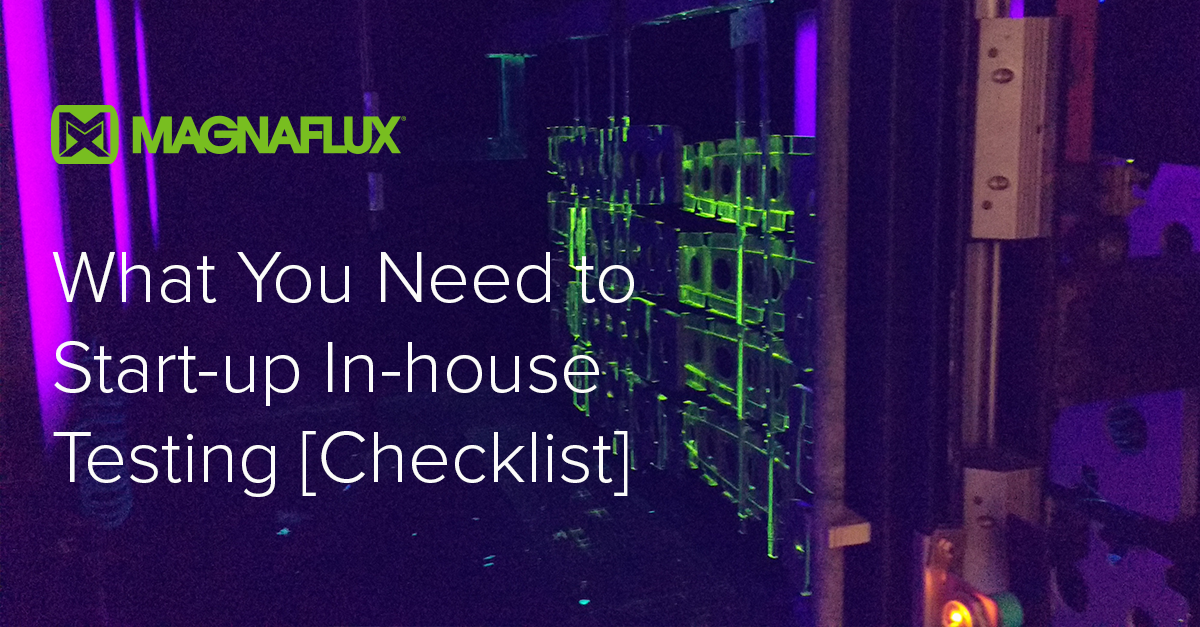
Taking your quality assurance inspections in-house can be a challenging but worthwhile endeavor. There are many factors to consider including effort level, cost, capability, drawbacks, and benefits.
Once the decision is made to bring testing internal, your organization will need to understand their unique quality assurance needs.
This article simplifies the checklist of the equipment, accessories, and materials you will need when establishing and deploying in-house nondestructive testing.
Implementation Process Overview
- For most organizations, NDT expertise is not often an in-house resource. Fortunately, there is a skilled community of experts who can help understand the unique quality needs of your organization. It is important to identify and collaborate with an accredited and responsible Level III to establish your quality system requirements. Learn more about Level IIIs here.
-
Another important factor for a new NDT program is to be aware of and understand what their industry’s governing specifications are and how those specifications are utilized. These specifications and certifications can address an entire organization or extend down to an individual inspection.
For example, ASTM E1444 or ASTM E1417 are commonly used standards which dictate magnetic particle and liquid penetrant inspection procedures, respectively. NADCAP is an industry-wide accreditation program used for auditing purposes in the aerospace supply chain. NDT standards can also be applied to personnel such as ASNT and NAS 410 or the aforementioned Level III qualification and certification. Yet more specifications can dictate the volume of inspections like ASME which requires quality inspections on 5% of production depending on technical requirements. In most cases with ASME, there is a 100% inspection requirement as most components covered by ASME are pressure related.
-
Once you have selected a consulting Level III and worked with them on identifying the guardrails and regulations that you need to conduct testing internally, you will need to generate and get approval on inspection procedures. These procedures will adhere to the requirements set within relevant specifications and instruct your quality team on how inspections need to be conducted.
In addition to working with a Level III on testing procedures, an organization can collaborate with certified Level I and IIs who will provide expertise on part processing.
- Now that your procedures and processing have been established, you need to identify and work with an NDT supplier or distributor who can provide equipment, materials, and consumables that meet your needs.
Want to make sure you have everything you need? Explore our checklists and guides here:
- Once the proper equipment and consumables have been acquired and properly prepared, an organization’s Level III and quality team should conduct a final review of procedure and processes using parts with known defects. This will ensure processes and procedures are identifying defects within expectations and specifications..
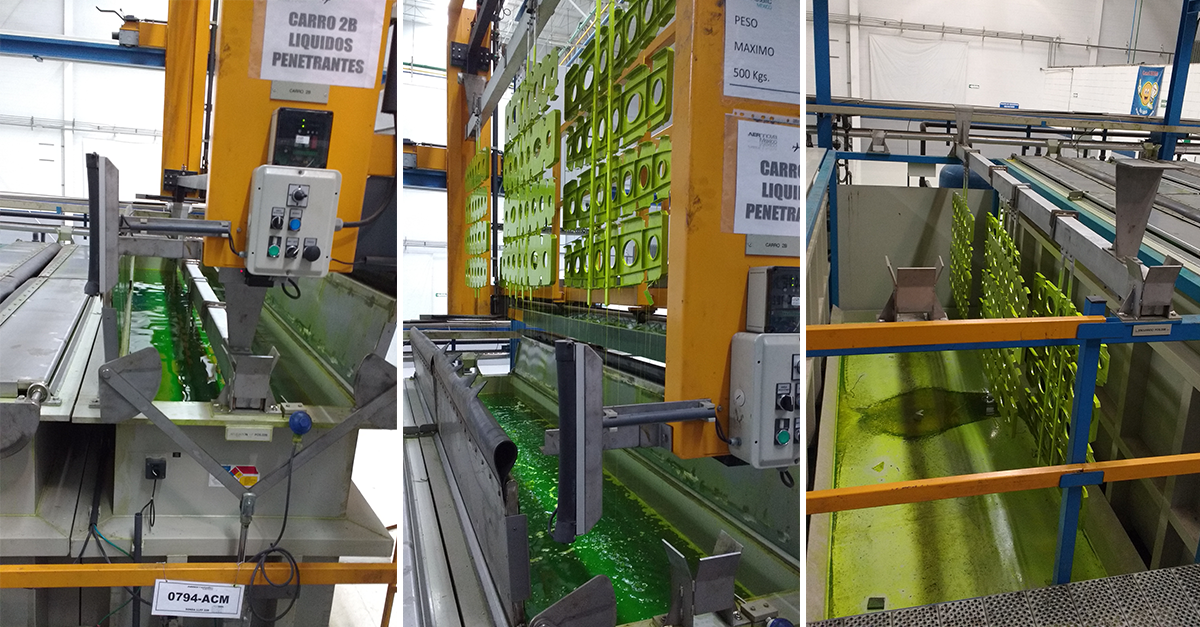
What to Keep in Mind
As you go through the process of setting up and conducting in-house NDT testing, there are several key things to remember.
First, it is critical to maintain records and have correct certifications filed. Keeping proper records provides several benefits. An organization can monitor its inspections to ensure quality. In the case of an audit, whether external or internal, having detailed records reduces risk and effort.
Audits are a concern for any organization conducting quality testing. If you do not have certificates on hand or certified personnel, any parts inspected by non-certified personnel could cause a recall of parts. Audits become even more critical if the inspections are for a third-party customer.
Magnaflux offers Certificate of Conformance (COC) certifications which you can find on the North American website and the European website.
Next, it is important to ensure equipment compatibility. This applies to both your facilities and the requirements of your inspections. Organizations should collaborate with their responsible Level III and collect their input during the purchase process to verify and select the correct equipment for inspections.
Finally, choosing the right partner is essential for organizations focused on quality. They need a partner who offers experience, expertise, and tools and who shares their focus on quality assurance. This alignment will enable an organization to have confidence in the tools and equipment they are using during their inspections.
Equipment Overview
In-house NDT testing requires a number of specific tools including specially designed testing machinery, inspection accessories, system performance monitors, and finishing equipment.
Each organization and testing needs are different, but regardless of procedures and circumstances, there is a common foundation of tools you will need prior to and during NDT testing.
Detailed below are the basic implements that you will need for magnetic particle or liquid penetrant inspection.
Magnetic Particle
- Mobile or stationary magnetic bench
- UV Lamp (fluorescent inspection only) & light meters
- System performance tools:
- Tool steel rings
- Centrifuge tubes and stands
- Hall effect meters
- Gauss meter
- QQIs
- Demagnetizer
- PPE for inspectors including UV-resistant glasses, gloves, and aprons
Liquid Penetrant
- Dip or spray station
- Rinse station
- Dryer station
- Developer station
- Inspection booth
- Drain
- Inspection materials
- UV lamp (fluorescent inspection only) and light meters
- System performance instruments:
- Known defect standards (such as panels or parts)
- Part handling tools:
- Baskets
- Trays
- Crane for heavy parts
- Timers
- Refractometers
- PPE for inspectors including UV-resistant glasses, gloves, and aprons
- Rinse water treatment equipment
Do you still have questions? Ready to get started? Connect with our experienced and knowledgeable team who can help you get started on your quality journey.
Contact Us