Penetrant system daily checks are necessary, and required by major industry specifications, to ensure the continued performance and integrity of penetrant materials and systems. The daily checks take only minutes to verify the performance of the penetrant inspection system. The checks can identify system components that may need adjustment to ensure continued conformance and prevent costly delays such as reprocessing parts.
1. Penetrant Contamination
Check penetrant materials for contamination such as precipitates, waxy deposits, or discoloration. Contaminated penetrant shall be discarded and replaced or corrected to reach an acceptable state prior to use.
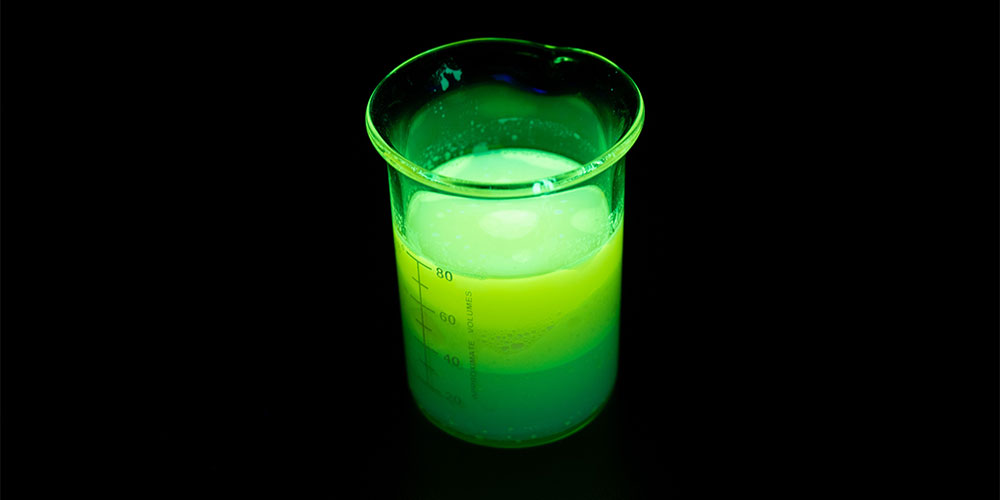
2. Dry Developer Condition
Check recycled or reused developer for fluorescence or caking. Dry developer should be fluffy. Caked developer should not be used and should be replaced. Dry developer that shows ten or more fluorescent specks in a 10 cm diameter circle shall be replaced. To learn about the available properties of developers and the relationship between dwell time and inspection quality, read more here.
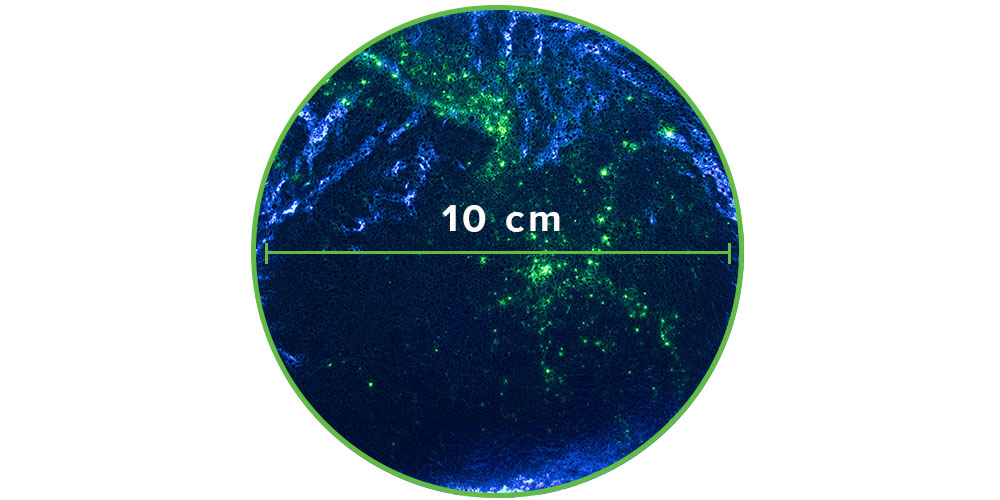
3. Aqueous Developer Contamination
Check water soluble and water suspendible developers for fluorescence and uniform coverage. Developers that show fluorescence or non-uniform coverage shall be replaced.
4. Penetrant System Performance
Process a known defect standard through the LPI system and compare results to the known defect standard processed with unused materials. If in-use penetrant material results do not meet the unused material results, further testing may be completed before discarding or correcting in-use penetrant materials. Over the past year, properly demonstrating the system performance check was the #2 Nadcap audit finding for penetrant systems. Learn what you need to do to comply here.
5. Blacklight Intensity
Check blacklight intensity daily and at initial use of blacklight. The minimum acceptable intensity is 1000 microwatts/cm2 at 15 inches / 38.1 cm from the front of the filter to the face of the sensor. UV LED lights shall comply with ASTM E3022. Most UV-A lamps on the market are set to provide 5,000 µW/cm2 at a distance of 15 in / 38 cm. To learn about these numbers, read more here.
6. Special UV Lighting
Check the UV intensity prior to use of UV borescopes, light guides, and light pencils. The minimum acceptable UV intensity is 1000 microwatts/cm2 at the working distance.
7. Examination Area Cleanliness
Check inspection area for fluorescent contamination and visible light levels. Clean inspection area if excessive fluorescent contamination is present to prevent contamination of inspected parts. Ambient visible light in the inspection area shall not be more than 2 foot-candles at the inspection surface.
8. Water Pressure and Temperature Checks
Check for proper settings for water pressure and temperature. Necessary adjustments to water pressure and temperature settings shall be made prior to performing penetrant inspections.
9. Air Pressure Gage Check
Check air pressure gages used in the LPI system at the start of each working shift.
These quick checks to verify acceptable results should be performed daily or at the start of each working shift to ensure the continued integrity of the LPI system.
Published October 16, 2018