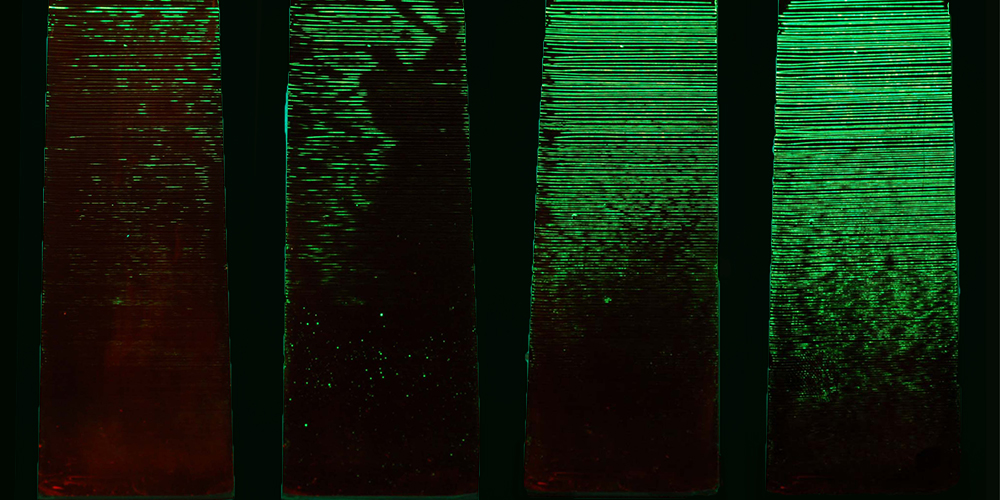
Sensitivity levels are a classification system for fluorescent liquid penetrants which is outlined in AMS 2644 Inspection Material, Penetrant specification. Sensitivity levels are not applied to visible penetrants.
AMS 2644 Sensitivity Levels
Level ½ – Very low sensitivity
Level 1 – Low sensitivity
Level 2 – Medium sensitivity
Level 3 – High sensitivity
Level 4 – Ultrahigh sensitivity
Reasoning for Different Sensitivity Levels
In fluorescent non-destructive testing there needs to be a balance between sensitivity and background fluorescence.
Higher sensitivity penetrants have the capability to detect smaller cracks and defects. However, higher sensitivity penetrants will have stronger background fluorescence. Excessive background fluorescence can interfere with the part inspection by making it difficult to identify penetrant indications. With excessive fluorescent background, penetrant indications may blend in with the background instead of standing out for easier inspection.
Lower sensitivity penetrants have less background than a higher sensitivity penetrant but they are not able to detect fine indications.
It is important to use a high enough sensitivity level to locate the necessary indications, while also keeping the fluorescent background to a minimum in order to maximize indication detection.
How Sensitivity Levels Are Set
If a penetrant manufacturer wants their penetrants qualified to and listed on the Qualified Products List, QPL-AMS-2644, the penetrant manufacturer submits samples of their penetrants to the Air Force Research Laboratory at Wright-Patterson Air Force Base in Dayton, Ohio. The Air Force Research Laboratory tests the penetrant and determines and assigns the sensitivity level based on the test results.
The approved penetrants are listed on QPL-AMS-2644 according to their assigned sensitivity levels and methods.
How to Determine Which Sensitivity Level to Use
The primary consideration when deciding on which sensitivity level penetrant to use is the guidance provided by governing specifications. Quite often, the penetrant sensitivity level is clearly stated in the working specifications for the process. This is particularly true when penetrant inspection involves safety critical parts. The specifications and standard operating procedures in use at a facility will dictate the penetrant sensitivity to be used.
If the penetrant sensitivity level is not already established by a specification or procedure, evaluation on actual parts with a few penetrants is strongly recommended. A lower sensitivity penetrant works well on rough surfaces, while a higher sensitivity penetrant is suitable for highly machined surfaces. Penetrant evaluation on actual parts is important to confirm proper sensitivity with acceptable background fluorescence to detect the type of defects typically found on the parts. Penetrant evaluation on actual test parts can also confirm proper processing parameters such as dwell time and rinse time.
It is possible that more than one penetrant sensitivity level will be used in a facility because of different parts, processes, and customer specifications in use at a given location.
Learn why penetrant removability is important, not just sensitivity here.