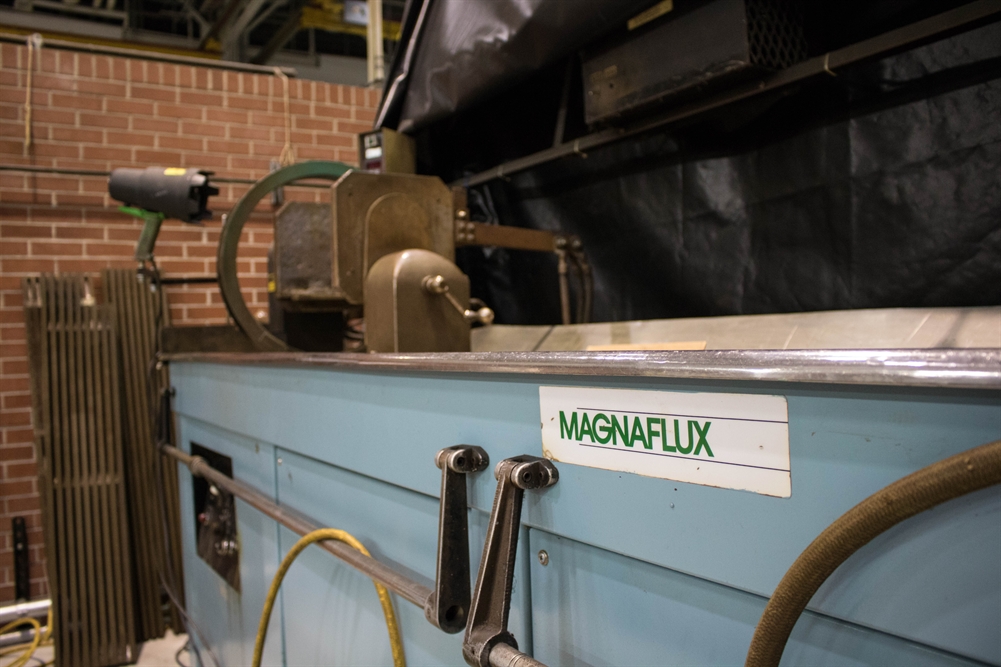
Just like changing the oil in a car, basic preventive care is a cheap and easy way for NDT professionals to get the most out of your mag particle inspections and make sure your mag particle machine investments last. Will it prevent all failures from occurring, no. But I can guarantee you that if you never pull off the machine’s ventilation panels to check the cooling fans or to blow off the dirt and dust off of the rectifiers, your machine will eventually develop issues, just like a car if it’s oil hasn’t been changed in years.
One of the reasons many NDT professionals don’t pay more attention to mag particle equipment maintenance is they perceive standards like ASTM E1444 as an operating guideline instead of as minimum requirements. While it is important to regularly have your meter calibrated for accuracy, your shot timer checked and to verify output repeatability, this is not enough to keep your mag equipment at peak performance.
I have seen times where the ammeter on the machine was precisely calibrated, within a much tighter tolerance than called for by the spec, but the waveform the machine produced (what is responsible for magnetizing the part) was not correct. In these cases, the companies absolutely knew what current was being applied to the part, but they didn’t know if the parts had been magnetized sufficiently or correctly. Who wants to take this type of risk?
The good news is that even if you haven’t been keeping your mag particle equipment in shape with regular maintenance, you can start doing simple maintenance checks right away.
Basic Equipment Maintenance
Daily operator checks
Every day the operators should perform visual inspections of exterior components of the magnetic particle equipment. Some elements to look for are wear on any wires or cables and lose connections on hoses and fittings
- Bath level: Make sure the bath is at the right fill level, add more bath if needed.
- Particle concentration: Check particle concentration with a centrifuge tube.
- Cable and bus-bar connections: Check coil, headstock, tailstock bus-bar and cable connections, tighten if necessary. Check wires and cables for worn or frayed insulation.
- Headstock clamping: Check headstock clamping action to make sure it is clamping securely.
- Locking devices: Check tailstock and coil lock to make sure they lock securely.
- Leaks (bath): Check tank, hoses and nozzle for leakage.
- Leaks (pneumatic): Check air cylinder, fittings, hoses, air regulator and speed valve for any leaks.
- Power indicator: Check that indicator lights are lit when power is supplied to inspection unit.
- Push-buttons: Check push-buttons for proper operation. Push-buttons are dimly lit when off and brightly lit when on.
- Digital ammeter and current assurance indicator: Check ammeter readout and current assurance indicator operations.
- UV lamp(s): Check for missing or broken filter or lamp. Check for damaged cord.
- Curtain: Repair small cuts and tears with black plastic electrical tape.
Weekly operator maintenance
Once a week the operator should clean the contact pads or plates and clean out the pump system. Cleaning debris out of the tank and changing the bath on a regular basis are critical to reliable inspections; pumps are good at circulating fluid and mag particles, but they don’t do so well with the paper towels, nuts or bolts that find their way into the tank.
- Contact pads and contact plates: If water bath is used, remove oxidation from between the contact pad and contact plate. Use a wire brush.
- Ground fault interrupt: Check for proper operation of UV lamp.
- Pump: Clean the sump screen to prevent loss of flow from the pump.
Monthly operator maintenance
Every month the operator should check and clean the tank, fans and air filter if necessary. Sometimes preventive maintenance may be a little bit more “preventive” in nature depending on the environment the unit is located in. For example, foundries and facilities with oily, greasy air need to look at their machines more frequently to minimize downtime. While our machines are great at detecting defects with mag particles, oily air and magnetic particles do not mix well with electrical components inside the machine!
- Tank and grilles: Check and clean if necessary. After cleaning, flush tank and grilles with appropriate bath solution.
- Fans: Listen for fan operation and check air flow for restrictions.
- Air filter: Clean air filter element and bowl.
- Pump seal: Check for deterioration and wear. Look for leaks of fluid around/near the pump/motor shaft
Advanced Equipment Maintenance
While most preventative maintenance is simple and easy to do yourself, there are periodically more advanced maintenance checks where you will want to bring in a trained maintenance professional. As an example, it is simple for a trained technician from a Magnaflux Authorized Service Center to verify waveform structure before they calibrate a machine, but most companies do not have the equipment or the expertise to perform this analysis themselves. Also, ASC technicians will be able to properly solve an issue if they see anything wrong during maintenance.
- Rectifier stack: Blow accumulated dirt from rectifier heat sinks and fan blades. Do not use cleaning solvents. Do not blow firing board.
- Control panel wiring: Check wiring for discoloration or burnt insulation, and that connectors are secure.
- Lower unit wiring: Check wiring for discoloration or burnt insulation and that connectors are secure.
- Transformers: Check transformers for discoloration and pungent odor.
- Connections: Check and tighten all connections, bus-bars, cables and wires.
- Tank and plumbing: Check for leaks.
- Fans: Check that the cooling fan(s) turn freely.
- Ammeter and “Mag” shot time: Check for accuracy every 6 months.
Want to learn more best practices for maintaining your magnetic particle inspection system? Download our tech paper on How to Maintain Magnetic Particle Suspension Baths.
The whole point of preventative maintenance is to make sure your mag equipment is at peak performance and doing the job it was designed for. I can tell you more than one story of getting a call from customers saying their machine is down and they need it up and running immediately, but they haven’t done any type of maintenance on the equipment (or even looked at it) in months, or years in some cases!
Preventive maintenance is not a one-time thing to check off the list, it is an ongoing process. How often it needs to be done will vary from machine to machine based on how often it is used and the type of parts being inspected, the more critical the part, the more often the maintenance.