Magnaflux co-founders, Alfred V. de Forest and Foster B. Doane, developed the magnetic testing method in the early 1930’s and it has been a core method of nondestructive testing ever since. However, even after being used by generations of NDT professionals, there are still some common areas of confusion or misunderstanding.
Here we set the record straight on 10 misperceptions we’ve seen in the field in recent years.
1. All metals can be used in Magnetic Particle Testing
What is the composition of your parts? It is important to understand what metals your parts are made of because only iron, nickel and cobalt can be magnetized. Most of their alloys and some forms of steels are also magnetic.
Aluminum is being used for an estimated 80% of aircraft materials today, because it is lightweight, strong, predictable and inexpensive. It is also one of the most common metals tested with magnetic particle inspection that cannot be magnetized.
If you are ever in doubt of the what can and cannot be magnetized, grab a permanent magnet and see if it sticks!
2. Your bath doesn’t need to be changed
Contamination is in every environment no matter how clean your space and parts are. Oils, greases, sand, dirt and other solids will be introduced to your bath by inspected components.
Oil in a water bath and vice versa is a primary concern as well. These unwanted contaminants can hinder testing performance and disguise indications.
Examine the carrier and particles during daily bath concentration checks. By looking for differences in color, layering or banding in either the carrier or the particles, you can spot contamination. If there is a band that fluoresces brighter than the bulk of the material, than there are excessive unattached fluorescent pigments and the bath should be changed.
The bath should be changed when foreign matter exceeds 30% of settled solids.
Dirt contamination
Water contamination
Dust contamination
Good Bath Example
3. More current is always better
Sending more current through a part is not always better.
If you hit a part with more amps you are less likely to see indications. This is because the fluorescent particles will not only be attracted to the flux leakages (indications), but to the entire part. This will create a bright background that hides the indications operators are looking for.
You do not want to saturate your field and mask defects because you need sharp contrast with the background of the part to easily spot indications.
It is important to work with a MT Level 3 to develop correct test methods that are part specific.
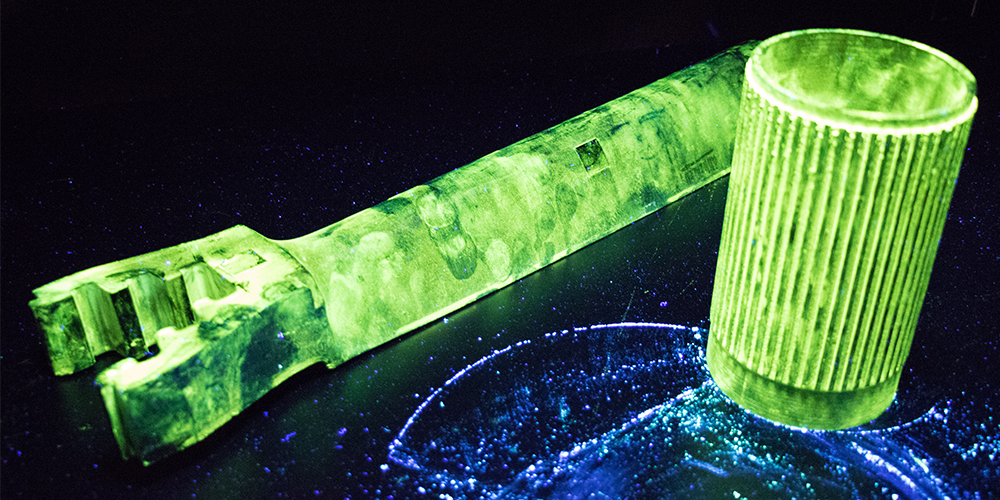
Parts with too much amperage used to magnetize them
4. All materials magnetize the same way
If parts look the same, but are made of different material, they will not use the same test method settings. This is because varied materials have different permeability and retentivity.
Permeability affects how easily magnetic current travels through the part and gets attracted to small flux leakages because of flaws. Retentivity of a material affects how well the material hold its magnetic field.
To ensure that parts are properly tested, double check the material and do not assume the same techniques can be used on similar looking parts.
5. Part cleaning is not necessary
Pre-testing part cleaning is a key part of the process to ensure the highest probability of detection. If you clean the part properly, it will decrease contamination to your bath and increase visibility of indications on the part itself.
Use a cleaner or remover to prepare parts before sending them to the magnetic particle testing area. Not only will this improve the quality of your inspections, but it can reduce the amount of times you need to change your bath.
6. You can mag through coatings
According to ASTM E709-15, “Thin nonconductive coatings, such as paint in the order of 1 or 2 mil (0.02 to 0.05 mm) will not normally interfere with the formation of indications, but they must be removed at all points where electrical contact is to be made for direct magnetization.”
Conduction coatings can mask discontinuities as well, and it must be demonstrated that the unacceptable discontinuities can be detected through the coating.
7. You must always do two shots
When looking for cracks in both the longitudinal and latitudinal direction, most machines require two shots. This is because the magnetic field that each shot produces will affect the other, which erases indications in one of the directions. There are two ways around firing two shots and inspecting a part twice.
The first is to only look for cracks in one direction. This is a testing specification decided by a certified level three, which depending on the part geometry and intended application.
The second way to avoid firing to shots is with a multi-directional mag bench. These benches have multiple phase circuitry that allow both directions of magnetic field to be applied at the same time without affecting each other.
If you care about high throughput and need both directions inspected for cracks then a multi-directional wet bench is the best option. It gets the job done in one shot and with one UV lamp inspection rather than two.
8. Daily system performance checks are not crucial
There is a reason that ASTM and NADCAP require quality checks to be performed and recorded.
Performing daily checks are crucial to ensure your bath and machine are in proper working condition. Operators must check specific criteria like bath concentration and UV lamp intensity daily or every shift. There are many more quality checks, like ambient white light, that can play a large factor in the inspector’s ability to see indications.
The daily checks can save time and money in the long run. There have been instances that an entire days’ worth of parts must be retested because the machine was not correctly calibrated and nothing got magnetized.
9. Adding particles makes it easier to detect indications
More particles are not better.
Adding too many particles to a bath will add too much concentration, and you will lose the ability to see small defects because of the excess background.
It is better to replace the entire bath and slowly add particles until the correct concentration is met.
10. Multi-directional units are always better
If you are only testing a few parts, it may not be worth the time to calibrate the machine for a multi-directional shot since an MD unit will only cut your time in half if you are processing parts in high volume using the same test method.
For complex parts in small volumes, it is better to go to a standard mag particle inspection unit and perform two mag shots.