What is a fluorescent magnetic particle?
A fluorescent magnetic particle is a mixture of three elements in which each component serves a particular purpose:
- Iron: provides ferrous material to force particle movement when electrically charged by magnetic fields
- Fluorescent pigment: what glows brightly underneath ultraviolet lights
- Resin: binds these two materials together and keeps them from breaking apart over time, ensuring that fluorescent material does not leak into the bath and cause excess background
Different types of particles are created by altering the properties of a particle by controlling various aspects of these three ingredients. The quality, amount, and blending method can all impact particle performance and characteristics. Magnaflux regulates the proprietary formulas and processes for creating fluorescent magnetic particles to ensure consistently excellent performance in every batch.
No magnetic particle product on the market is a single particle size.
Here is an example of one of our products, MG-410, magnified to see the details of the particles. Some areas are pigment (yellow - what makes it glow!), the metallic is iron (what makes it attract to indications), and the resin that holds each piece together. Note that the resulting particles vary in size from small fragments to larger clusters of material.
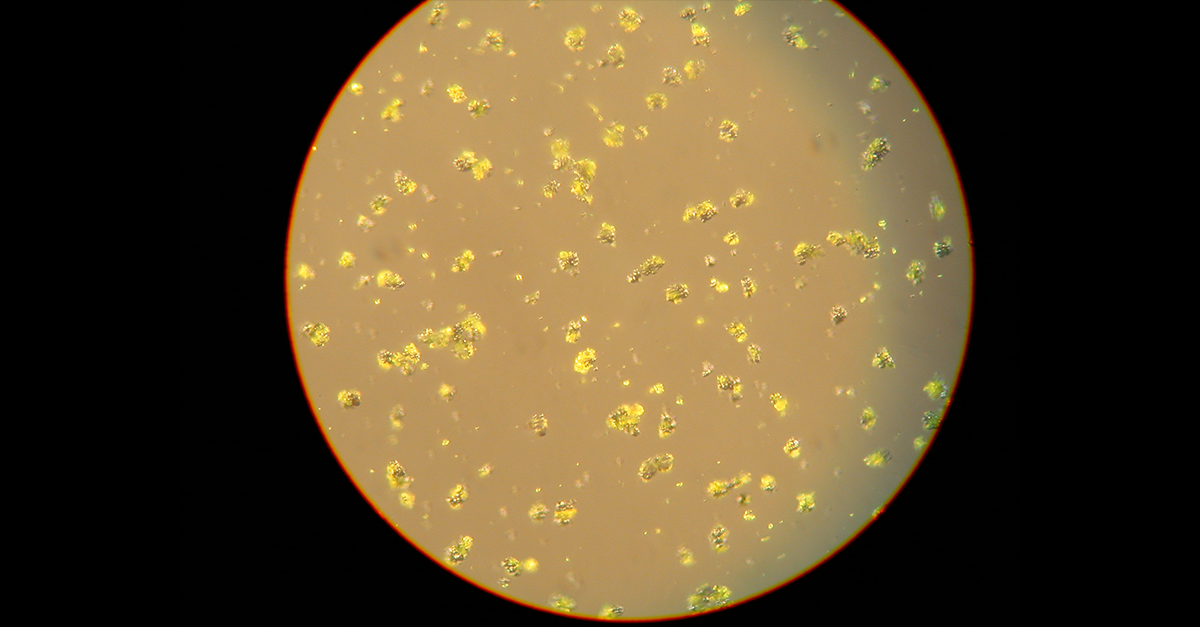
No magnetic particle product on the market is a single particle size – they all have a range of particle sizes, with some being smaller on average and others being larger on average. Typically, what is reported on product data sheets is the product's mean particle size, but particles can vary widely in size around that mean.
Here is a microscope image of 14A magnified to 400X. Notice the distinct differences between these particles and compare it to MG-410. These differences are not just limited to mean particle size but also particle size distribution, type of iron and fluorescent pigment ingredients, and ratios of pigment / iron / resin. Additionally, the process to create these particles varies as well. All of that in combination results in two particles that both perform excellently, but for often different purposes and applications.
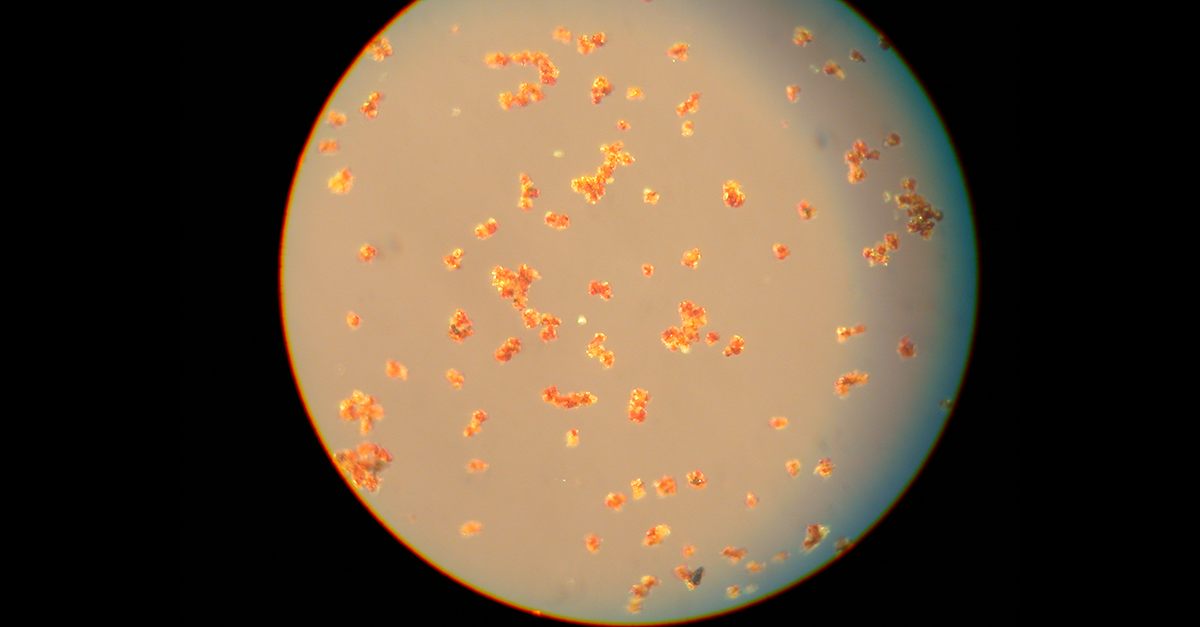
How big is a micron?
Mean particle size for magnetic particles is typically a measurement in microns or micrometers. To understand how small these things are, here is an image showing a 6-micron filament lying on top of a human hair. See how thin that filament is? That 6-micron diameter is around the typical mean particle size claimed on most fluorescent magnetic particle datasheets. You can see how small these particles are and how tightly you have to control the process to get even 1-2 micron differences in mean particle size.
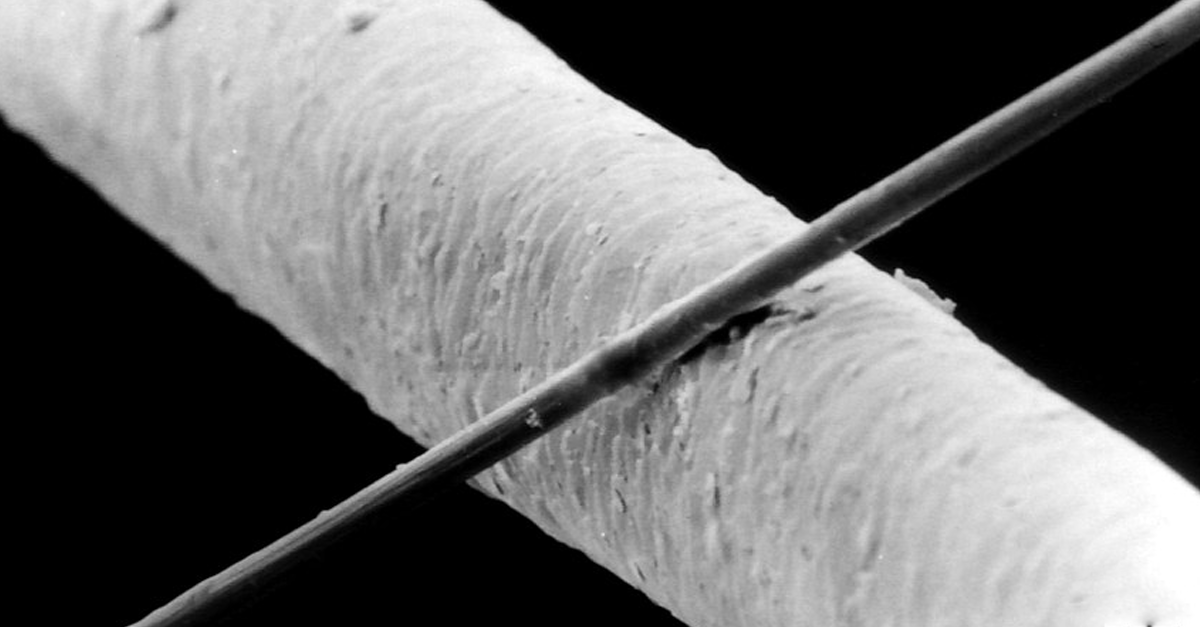
Does particle size matter?
Controlling mean particle size is undoubtedly a critical factor in magnetic particle performance; however, it is not the only characteristic that matters. Particle size distribution, quality and quantity of pigment, the ratio of resin used, and quality and quantity of iron are all essential factors that can alter the performance of a fluorescent magnetic particle. Selecting a particle purely based on a mean particle size listed on a product data sheet is unlikely to get you the best performing particle for your application.
We ran some of the top-selling fluorescent magnetic particles on the market through an experiment on a Tool Steel Ring to test this. We magnetized the ring and applied material in the same way for every product and then counted the number of visible indications on the ring for each, per ASTM E1444 standards. We found that particle size has no correlation with performance, and smaller particles don't necessarily get you better results. The chart below shows the resulting data:
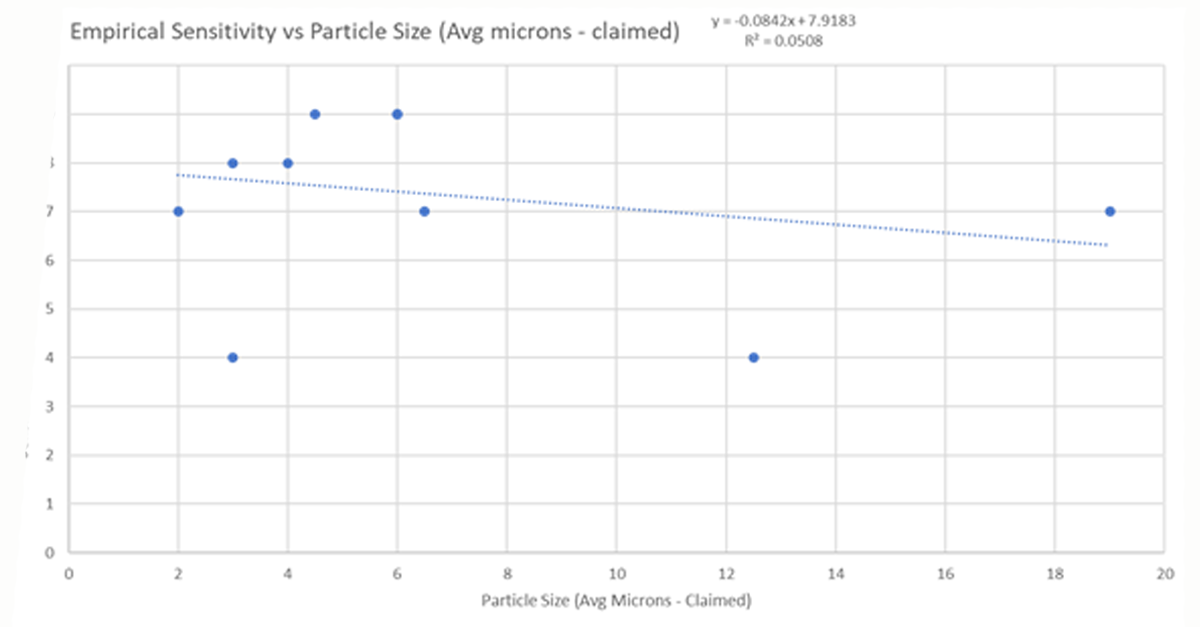
Note the R-squared value of 0.0508, which suggests that only ~5% of the variation in Sensitivity is determined by the variation in claimed mean Particle Size. Here we define "Sensitivity" as the number of visible indications on the Tool Steel Ring. It is clear from this chart that, based on our test results, particle size does not determine the performance of fluorescent magnetic particle. Also, note that some of the -performing particles claim to have very small particle sizes (2-3 microns). To check whether differences in how particle size is measured between manufacturers may have skewed our data, we ran the particles on a Horiba Laser Particle Size Distribution Analyzer and plotted that against our Sensitivity data:
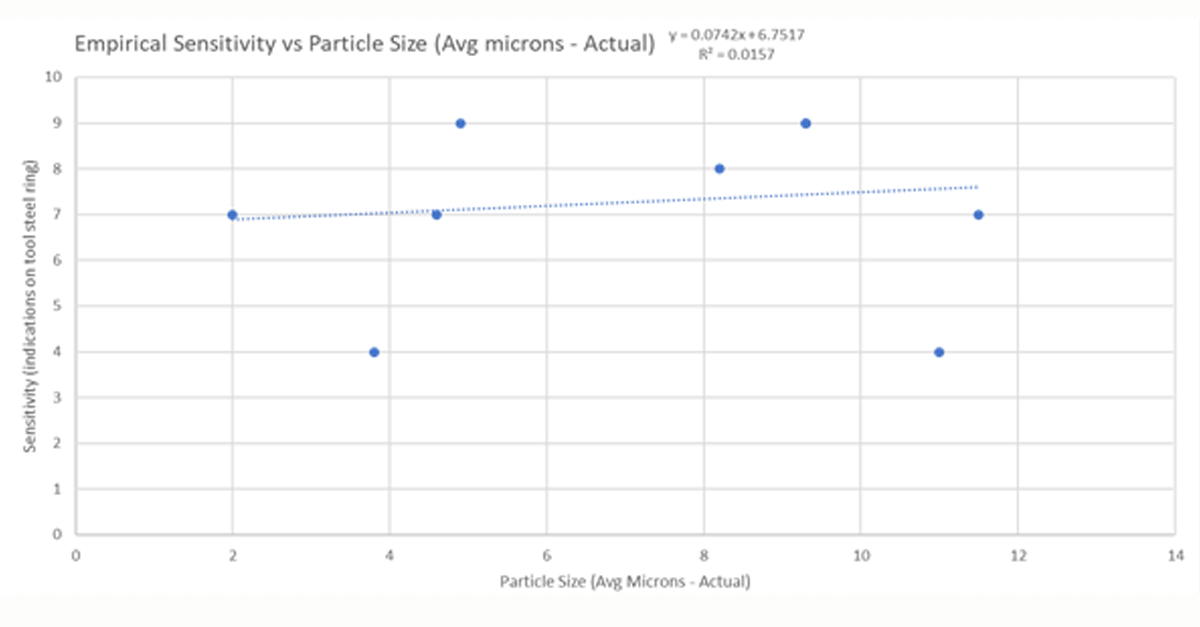
Here again, there is no real correlation between the variables based on this data. This suggests that purely selecting products based on particle size will not give you the best performing fluorescent magnetic particle.
So, how do I find the fluorescent magnetic particle that is right for me?
Our test data showed that particle size is not the only factor that determines the performance of a fluorescent magnetic particle. But you may be asking, well, if that is the case, how do I find the correct particle for the job?
As we mentioned earlier, many aspects of a particle factor into its performance. Additionally, the importance or impact of those differences can be different depending on the application and types of parts in a test. That is why we recommend that the best way to find the correct particle for the job is to test it on actual parts in application conditions. With so many variables that go into how a particle performs, application testing is truly the preferred method for finding the best match.
Published January 11, 2022