5-question guide to help understand the differences between Level 2 penetrants.
How do I decide which penetrant is best for my application? In many manufacturing environments, the responsible Level 3 will specify which penetrant is used for an application, based on their extensive expertise and training. This guide can help to sort through the options and understand the differences among the Magnaflux products in the Type 1 Level 2 penetrant lineup.
For more information on selecting which overall method is best for your application, please check out this blog.
1. Do your specifications require a water-washable or post-emulsifiable penetrant?
Based on the specification you are working under and the types of parts and applications you are dealing with, you should understand whether a post-emulsifiable penetrant system is needed or if a water washable penetrant will do the job.
If you need a post-emulsifiable penetrant, the choice is simple since Magnaflux has one sensitivity Level 2 option: ZL-2C.
Read more information on water-washable vs. post-emulsifiable penetrant systems here.
2. If you require a water-washable penetrant system, what is your most important desired outcome?
Water-washable Level 2 penetrants have additional properties that make selection more complicated. The option can be divided out into 3 simple categories based on the desired outcome. The first desired outcome is (A) maximized product performance with the highest sensitivity, the second is (B) minimizing penetrant usage and the third is (C) minimizing environmental hazards and waste-water disposal costs.
A. Maximize product performance and level 2 sensitivity, particularly for inspections governed by aerospace specifications.
Aerospace approved products require strict certifications and sensitivity properties. For example, ZL-60D is a high-performance Level 2 penetrant and is the only Magnaflux North American water washable Level 2 penetrant approved by Pratt & Whitney for aerospace applications. ZL-60D delivers excellent compatibility and performance on aerospace materials, including aluminum, steel, nickel, and titanium.
B. Minimize penetrant usage and decrease the overall cost of quality with superior drag-out and removability properties.
Reducing drag out, or the amount of penetrant left on a part after it is dipped and allowed to dwell, is a growing requirement for automotive manufacturers looking to control costs without sacrificing product performance. Reducing drag-out means that less penetrant remains on the part, which leads to a decrease in penetrant consumption. This allows customers to get more use out of a single drum or tote. ZL-150 is designed to deliver excellent level 2 sensitivity and strong removability while decreasing drag-out. This combination of properties lowers the cost of quality by enabling teams to reduce rinse water volume, use less penetrant, request fewer purchases, and minimize product changeover with maintenance teams.
C. Minimize environmental hazards and waste-water disposal costs.
Reducing waste-water pollutants and environmental footprints are requirements for many global manufacturers and EH&S teams. Waste-water disposal may require special handling, which can be costly. ZL-440 reduces environmental and health hazards as a water-based Level 2 penetrant with low BOD & COD levels. Low levels mean customers can potentially save on water treatment or disposal costs, depending on local regulations. Note that this penetrant is used under a separate method (Method A(W)), and additional testing and maintenance is required for water-based penetrants, per specification requirements.
For a more visual depiction of the Magnaflux Level 2 sensitivity penetrant options and benefits, see the diagram below:
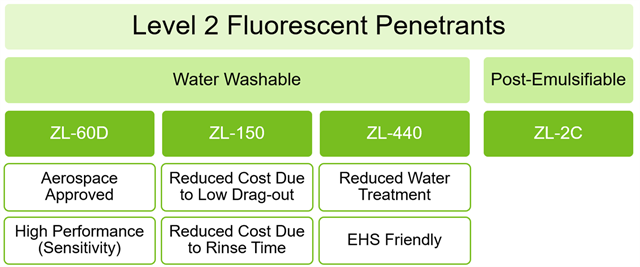
For more information or to help select the right penetrant for your application, please view our website or contact our customer service team.