Please wait while we gather your results.
Related Blog Posts
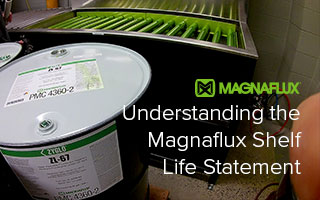
Answering popular questions regarding shelf life for magnetic particle and liquid penetrant products used in nondestructive testing
Read More...

A real-life approach to understanding industrial aqueous cleaning before and after nondestructive testing
Read More...
![What You Need to Start-up In-house Testing [Checklist] What You Need to Start-up In-house Testing [Checklist]](/Files/Images/Blog-Images/03162021-Titan-Thumbnail.jpg)
Step-by-step process listing everything from the equipment needed in magnetic particle testing and liquid penetrant testing to preparation for NDT audits
Read More...
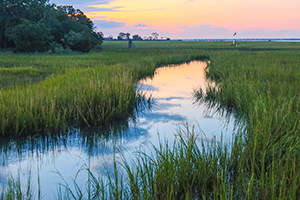
As the NDT industry continues to modernize and evolve in the 21st century, sustainability has become a hot topic. For suppliers and consumers of NDT products, evaluating and adjusting processes and products, investing in innovative technologies, and putting sustainability at the forefront are critical.
Read More...
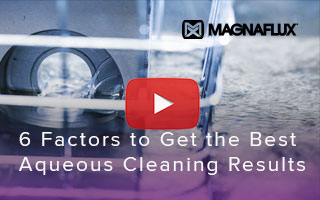
In this article, we will go over the six key factors to a successful cleaning process and give you some Pros & Cons to consider for each
Read More...
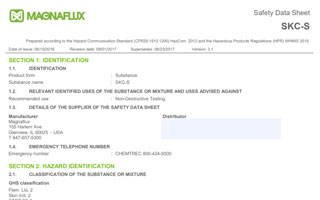
We highlight the 5 major sections to understand on a Safety Data Sheets (SDS) in accordance with US OHSHA Hazcom 2012 GHS regulations
Read More...
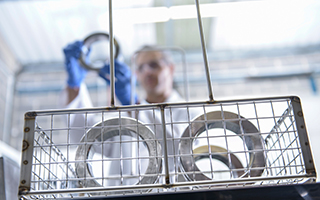
5 steps to identify and solve a NDT aqueous cleaning issue, and a troubleshooting guide with common problems + solutions
Read More...
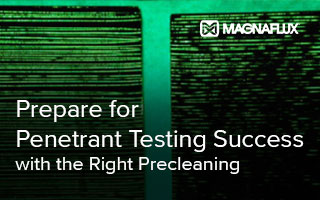
Learn why proper precleaning before liquid penetrant inspections can make or break your nondestructive testing results
Read More...