Getting consistent, quality results from penetrant or magnetic particle fluorescent inspection systems depends on many factors; and even if all the parameters are exactly correct (concentrations, dwell and wash times, amperage, waveform, etc.), poor UV-A lighting leads to difficult and inconsistent inspections.
Variation in the UV-A intensity and coverage during final inspection will significantly impact the number and type of indications that can be found. This makes the critical job of evaluation even harder.
Magnaflux is working with our customers to better understand the issues that end-users face. Below, we explain the challenges one high-volume automotive casting manufacturer faced, and how Magnaflux helped address their challenges.
About the Customer
This customer operates a high-volume manufacturing facility making large, cast parts for the automotive industry. The parts are inspected using an automated penetrant inspection process, with the inspectors working in a dark room with parts travelling along a conveyor. The inspectors use a combination of overhead and handheld UV-A lights for inspection.
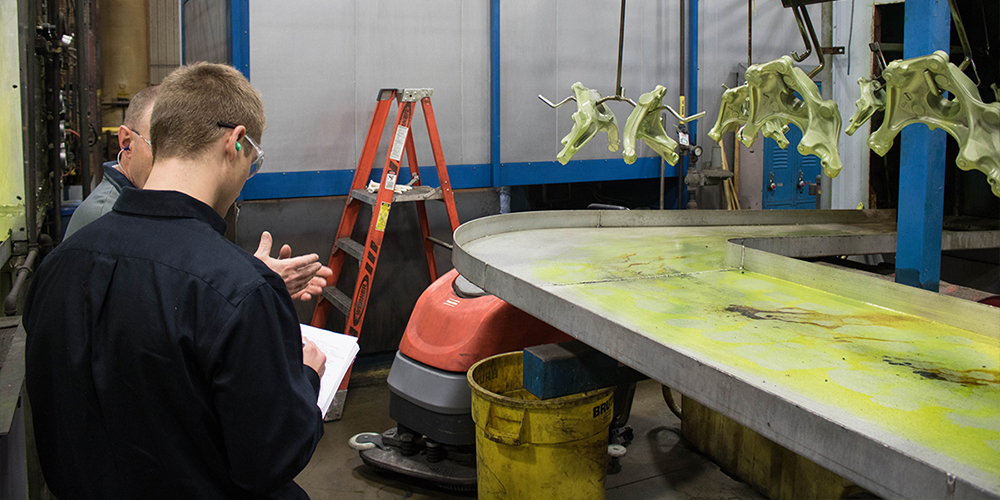
Challenges
The long inspection line was originally built with nearly a dozen fluorescent tube lamps to provide UV-A irradiation to inspect large automotive castings.
Significant cost in maintaining the lamps prompted them to look for alternatives, and recently they had changed out some of the fluorescent fixtures with LED lamps. The LEDs provided good intensity, but the beams were narrowly focused and did not cover a single part completely. This meant that the inspectors had to move the part around to look for indications, occasionally resorting to additional hand-held lamps to complete the job.
Solution
Magnaflux engineers evaluated the inspection area, and replaced some of the remaining fluorescent lamps with ST700 stationary overhead LED UV lamps. The ST700 units were spread apart and angled towards the parts to provide the maximum coverage possible while still maintaining intensity at desired levels.
The lights were left in continuous production for 6 weeks so that the inspectors had time to evaluate them in real world conditions and compare to the competitive LED and fluorescent products.
Results
Compared to the other lamps already installed, a single ST700 provided as much coverage as three of the other LED units. This allowed the inspectors to see the entire part without excessive handling, making it easier to complete their examination.
Another benefit came from the ST700’s high-intensity UV light, which allowed the lamps to be positioned off to the side of the gantry crane moving the castings through the inspection area, while maintaining full inspection intensity. The combination of high-intensity UV-A with wide beam area meant inspectors did not need to resort to hand-held lamps to supplement their examination and they reported significant improvements in ease-of-inspection and evaluation were reported.
An unexpected benefit was found towards the end of the beta test – elimination of safety hazards in the inspection line. Maintenance of the older fluorescent tube lamps required special procedures because of the weight and positioning of fragile bulbs and filters. Those hazards and special procedures could be eliminated through the use of the ST700.
Conclusion
Swapping out mercury-vapor lamps with UV LED fixtures can present their own challenges, often trading off between intensity and beam area. The ST700 Stationary UV-A Lamp provides both high intensity and large beam area to address those challenges.
With the ST700, significant improvements can be made in the consistency and reliability of inspections, while increasing the safety and ergonomics of the system as a whole.