Magnetic Particle Inspection benches are built to last. It is not uncommon to see equipment that is over 50 years old and still in use today. The longevity of the equipment is undoubtedly a combination of the durable craftsmanship put into manufacturing the unit and the many years of upkeep and maintenance by the NDT technicians. When it comes to Magnaflux equipment, the team in DeWitt, Iowa, that builds these machines takes great pride in their work and does not compromise when it comes to quality. Magnaflux chemical materials are designed and manufactured to help optimize the inspection process, and the chemical properties such as corrosion resistance ensure that equipment investments survive demanding and harsh environments.
Corrosion Protection
Just like routine oil changes in your car help keep your engine humming, Carrier II does an excellent job of keeping the MPI unit functioning at its’ top possible output. Carrier II protects the bench from corroding, protecting the equipment investment, and reducing maintenance and downtime. The below example is a unit from 2005 filled with a water bath.
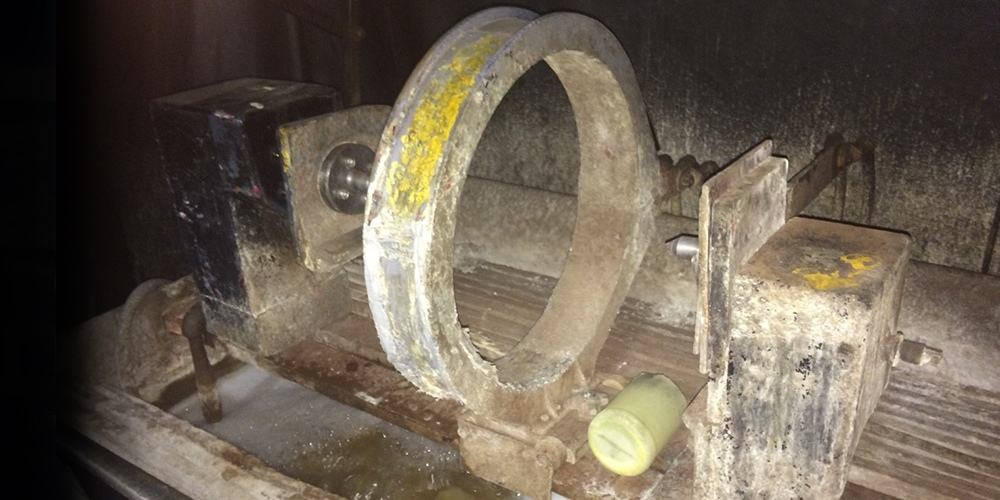
This result is typical in all units that are using water in the bath to save some upfront costs. Corrosion begins immediately when a unit is subject to sitting water and can force damage components and dissolved and investment in the new equipment relatively quickly.
The comparison of a unit from 2005 is shocking but understandable because the Carrier II protects your equipment rather than corroding it due to being an NDT-approved fluid that is tested and verified to safe-guard equipment parts. Switching to a carrier oil that provides corrosion protection can double the lifetime of your equipment. Check out more of the photos below to view the damage of corrosion on MPI benches.
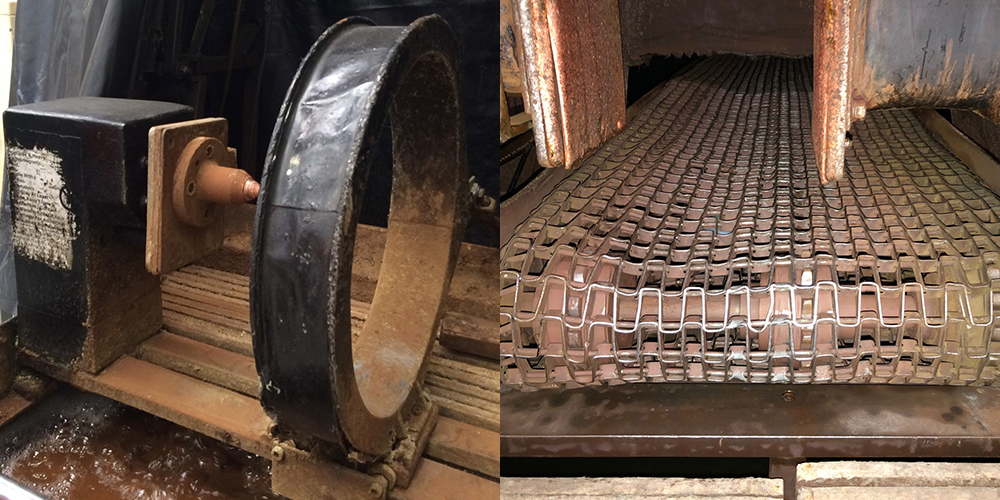
The benefits of Carrier II are proven time after time by not only increasing the efficiency and accuracy of inspection but by protecting your equipment and the particles in the bath as well.
One look at this unit built before 1980 is a dramatic realization that Carrier II can genuinely protect your equipment and more than double the usable lifespan.
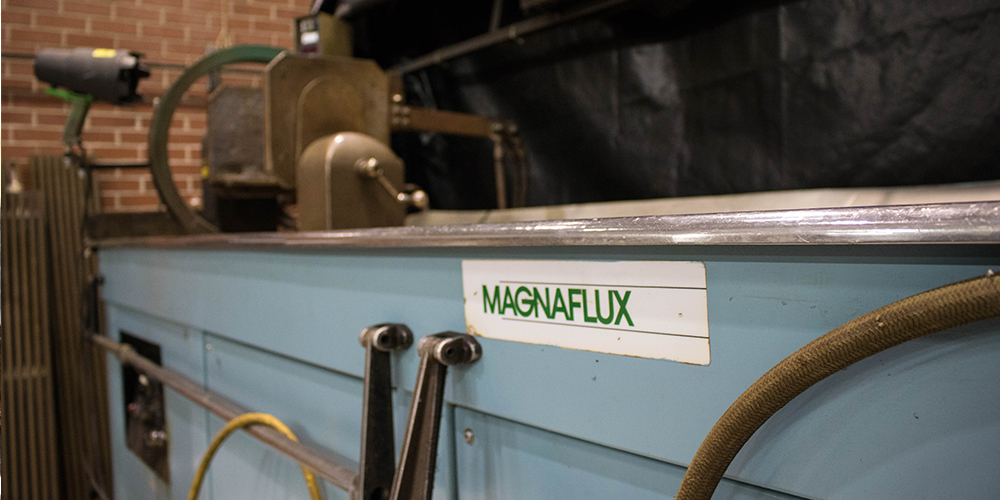
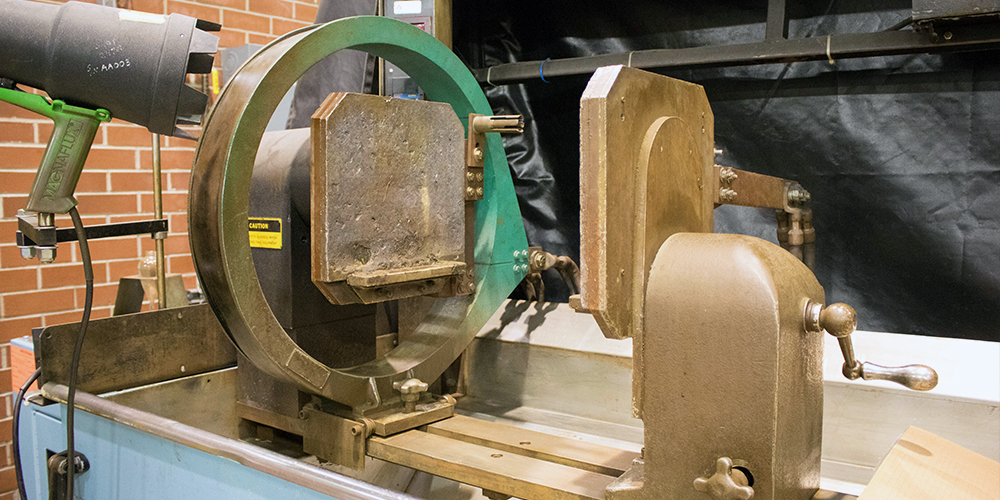
Decrease Maintenance
Carrier II baths last longer due to slow evaporation, and they are also less susceptible to contamination from bacteria or fungus. More importantly, Carrier II protects magnetic particles from wear and tear and keeps them evenly dispersed in the bath.
The viscosity of Carrier II is not only optimized the wetting of test surfaces but also limits the magnetic particle drag out. Water moves faster over the part without keeping the 14A magnetic particles with it, resulting in more left-over particles on the part, without a vehicle to provide particle mobility.
Inspection Flexibility
Expanding the scope of possible inspection applications can significantly increase your top line. Carrier II is approved for all major international magnetic particle testing specifications, including A-A-59230, AMS 2641 Type 1, ASME BPVS, ASTM E1444, ASTM E709, ISO 9934, NAVSEA 250-1500-1, NAVSEA T9074-AS-GIB-010/271.
Safety
Inherit danger of using non-NDT petroleum-based oils for NDT can be costly. Some non-NDT petroleum-based oils may contain ingredients or impurities which cause corrosion or hydrogen embrittlement over time.
To learn more about what an NDT-approved carrier is, safety benefits, and what sets it apart from commonly used, non-approved base oils such as Isopar M or kerosene read our Frequently Asked Questions About NDT Carrier Fluid.
Published February 25, 2020