Quality assurance is the most important objective to avoid catastrophic failures and severe loss of life in the NDT industry. Complete confidence in tested parts becomes increasingly difficult to maintain as pressure builds on NDT operators and managers, who are expected to increase part throughput while also expanding test flexibility to a much wider range of parts.
Non-destructive testing facilities are responsible for assuring that any part to come through the door is properly checked and tested, because lives are on the line. Efficiency typically suffers due to the stress on quality assurance, and rightfully so.
More Parts = More Techniques: Technique Management Challenges
Some NDT facilities have started to migrate to electronic methods of data recording, but very few have eliminated paper all together. Similarly, technique sheets are generally either stored in binders or in a network folder shared throughout the company. This makes it relatively easy to search by customer name or part number, but it still requires an operator to manually look up the technique and set the machine parameters accurately. Not only does this time add up, but it introduces the chance for mistakes.
There are an immense number of factors getting boiled down to create each technique, which defines exactly how the operator must test each part. Recipes are specifically what is being put into the machine (current, amperage, shot type, timer), while techniques include all recipe settings and instructions (part orientation, central conductor, acceptance criteria, etc).
Communication of updated techniques and training on how to properly setup machines is often too overlooked in this industry. This is such a crucial part to attain correct results that no company can afford to make mistakes.
To understand how to deal with high part variability, one must first understand how techniques are created and how that translates to operators and the recipe parameters set on any machine.
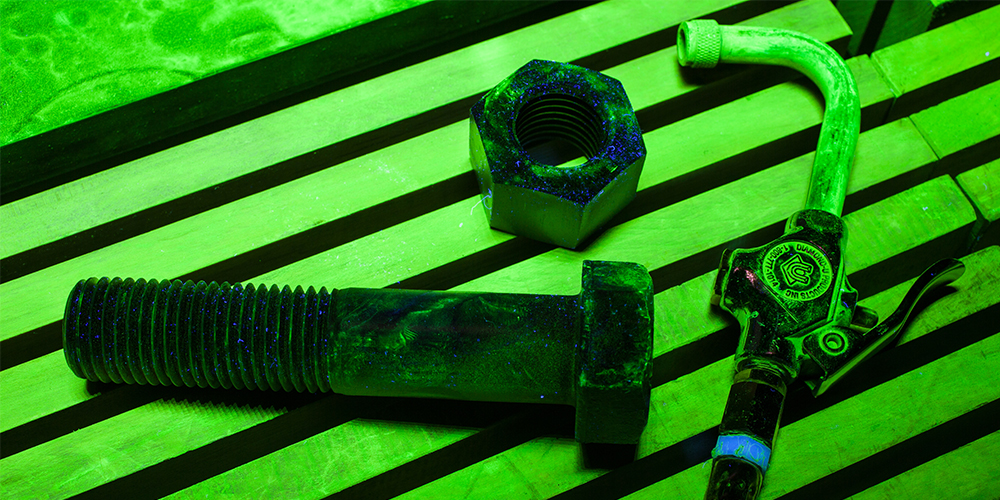
5 Key Elements for Successful Magnetic Particle Inspection
- Proper understanding of the applicable codes, standards and specifications agreed upon
- Procedure written by an ASNT Level III based on the above factors
- Validation of process via demonstration by qualified personnel, calibration of equipment and known discontinuity sample testing
- Test performed by qualified MT personnel
- Records of test reports and detailed quality control logs
These elements require frequent attention to keep up with industry demands and customer directives. Operators and quality managers must stay vigilant to use the most current techniques, especially when the parts being tested are highly variable.
These techniques are for individual parts, but the machine recipe, specifically amperage, may need to be adjusted to meet gauss requirements when changing over to a new machine. This is due to age of machine, make, model, and many other factors like connection surface area.
Reasons for Different Techniques
There is no way to get around the fact that many techniques will need to be written. Each part requires very specific techniques due to reasons listed below and many more.
- Material composition
- Manufacturing methods (i.e. Casting vs machining)
- Size and shape of the part
- Critical failure locations on part (Irrelevant Indication spots)
- Diameter changes (Multiple shots required)
What can be changed is the way in which these recipes are used and communicated. The cost of not having technique sheets in a convenient, easy to use database system will grow as test repeatability and part complexity become bigger concerns.
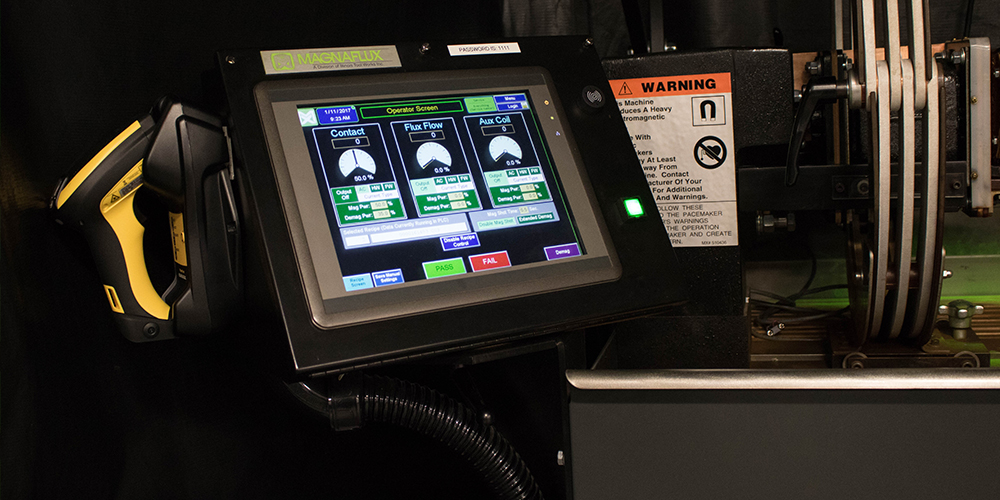
Simplify with Integrated Techniques
Testing more parts ultimately increases operational complexity, from the increased amount of technique sheets to the time spent adjusting machine parameters for each new part.
This complexity can be significantly reduced by utilizing integrated techniques and the new barcode system. Quickly scan your next job in and begin the next test thanks to the preset machine parameters. No need to search through files looking for techniques, because this database system can store up to 1000 individual recipes right on the machine itself.
Take a closer look at why this system is the best way to deal with part variability.
1. Improves Quality Control Traceability
Test parameters stay consistent, inspection date and time are recorded, part number is traced, and technique name and number is tagged on.
2. Minimizes Time to Process Parts
Rather than finding a recipe in a large binder or clicking through files, any operator can easily search a database via part number to pull up any part technique and recipe. This becomes more valuable the more an operator must change parts throughout a shift, as well as for less experienced operators.
3. Minimizes Operator Error
Integrating recipes onto the machine takes away any chance for a forgotten parameter, or accidental mistake by an operator during part setup and evaluation. When the database automatically sets machine parameters through a stored recipe, the risk of wrongful testing or acceptance is reduced significantly.
4. Easier File Management
Recipes are locally found in one location and tracked by any factor you desire giving clear data on how parts were testing. This also allows for recipes to be updated remotely, which improves manager efficiency and lowers the risk of an operator overlooking a change.
5. Future Focused
Maintaining recipes on a database will allow for easy updates and additional techniques that can be exported to any file and communicated very quickly. This first step towards a smarter machine will make any future process improvement even easier and more beneficial.
Tips to Get Started
- Ask yourself where your mag particle process should be in 5 years, you can use these questions to start generating ideas:
- What are the two biggest challenges you currently face in your NDT department?
- What new jobs or projects are you expecting to take on in 2018? In 2019?
- What challenges do you expect to see in terms of resources in the next 5 years? These can include personnel, budget, expertise, etc.
- What major shifts do you expect to see in your industry? Are parts becoming more complex, are new materials being used, are new regulations or specifications starting to be used?
- Check out “Database System for Mag Particle Wet Benches [Video]” to learn more about how to improve process control and efficiency
- Subscribe to emails from Magnaflux to stay up-to-date on the latest news in mag particle testing