MPI has been a long-standing staple in the NDT industry. As one of the most reliable testing methods for ferrous parts, it is still in high demand. As the demand grows for more and more parts to be tested, testing facilities face capacity issues. Below are some of the best and easiest ways to improve the efficiency and reliability of your MPI process.
1. Improve UV lighting
A good UV lamp can be the difference maker in any inspection using fluorescent particles. The probability of detection increases significantly when inspectors have a bright and even beam intensity on parts.
The two typical options for lighting are either a hand-held UV lamp or an overhead UV lamp. The hand-held lamp is perfect for parts that require a moving light to traverse the surface of the part in various directions. An overhead lamp is great for high speed production and provides a larger coverage area to see indications with no hands needed.
Switching mercury-vapor lamps to UV LED lamps has become an easier transition. There is no longer the trade-off of beam intensity and beam area. There are also other benefits to having UV LED fixtures in place, like less heat radiation and improved energy efficiency.
Choosing a light is application specific, but UV LED lamps with intense and even coverage can make any inspection process faster and more reliable. To read a case study on how LED UV lighting improved inspection speed click here.
2. Save recipes on the mag bench
Every part tested on a mag bench needs a specific recipe, which includes parameters like current type and amperage. Saving these recipes directly to the mag bench and recalling them later can save operators time and improve test repeatability.
This is especially true for processors that are frequently switching jobs or test the same parts on and off. Rather than traveling to search through binders or computer files, pulling up a part recipe can be as simple as scanning or typing in a part number on the operator screen to automatically set the correct testing parameters.
The process of saving a recipe onto the machine eliminates any chance of technique sheet misinterpretation or accidental operator input mistake. A level 3 could set up recipes and ensure that each test is done with the same parameters.
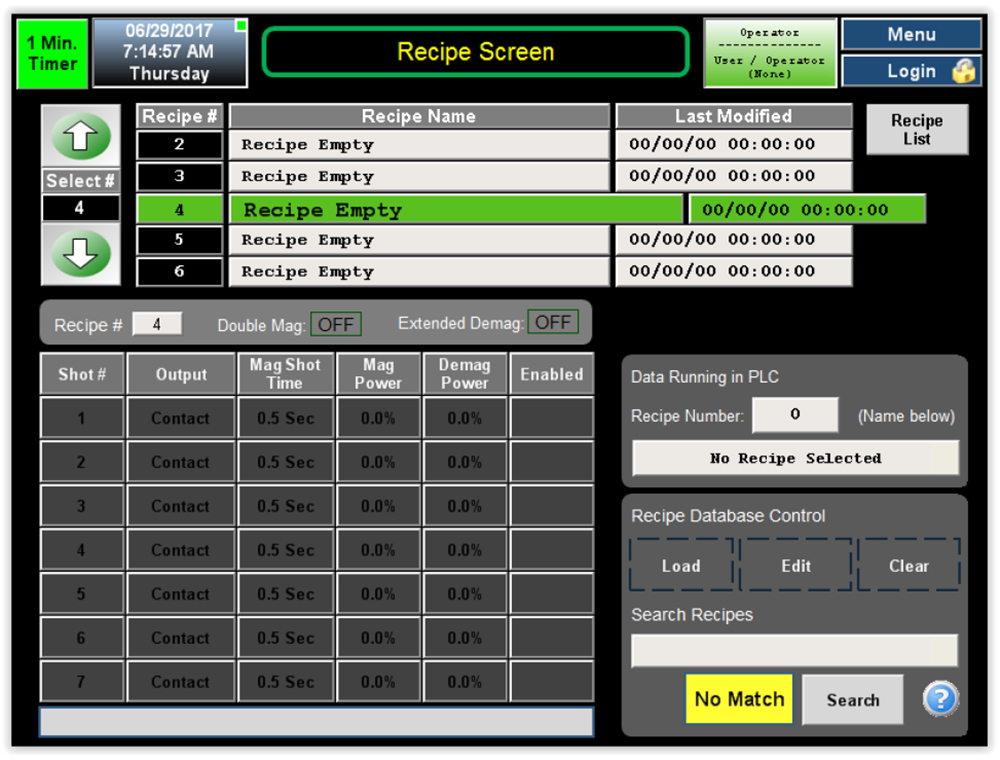
By utilizing the ability to save recipes to mag benches, your process can be more repeatable and efficient. Maximize test repeatability with consistent current and amperage settings, minimize test set up time with quick search, and mitigate operator error with automatic settings for each recipe.
3. Use multi-directional machines
If your parts require total inspection, then your process should include a magnetic particle bench with multi-directional capabilities. Multi-directional is a term that indicates the ability for a magnetic field to be induced in both the longitudinal and circular directions at the same time, without interfering with each other.
This capability has been proven in time trials to make magnetizing a part with multi-directional machines up to twice as fast as using a traditional uni-directional machine. An inspector only needs to mag and inspect with a UV lamp one time, as opposed to repeating the entire process again for indications in the opposite direction of the first check.
This brings tremendous benefits to high production and variable part production facilities alike. A multi-directional machine provides serious production value by testing two parts in the same time as most machines could only test one.
4. Electronically record results on machine screen
Anyone in the magnetic particle inspection industry must maintain detailed quality control logs and testing records. This task often falls on individual operators and their managers. What if there was a way to do this more efficiently and with more reliability than a clipboard next to the machine?
Well there is! Mag benches integrated with database systems can store all the required quality and testing data you need. The touch-screen interface allows operators to easily enter data. This database can transfer data and output everything needed in a customizable format.
5. Automate part processing
Introduction of automation can speed up the magnetic particle inspection process and increase reliability by eliminating human error.
Recipe selection and test setup can be automated by scanning a barcode on your part traveler, which then tells the machine exactly which part it is and which recipe to use.
Custom machines can also automate part processing so all that is needed is a visual inspector. A programmed arm can grab parts and place them in between the contact pads. Then the mag machine automatically clamps, bathes, mags and unclamps the part. This part then leaves the booth on a conveyor to a separate inspection booth, where it is manually checked for cracks and sent through a demag coil.
Automating simpler aspects of your process can speed up inspection time and allow your operators to focus on more crucial tasks.
Conclusion
The NDT industry has relied on magnetic particle inspection as one of the best and most reliable methods to test ferrous parts for flaws. Advances in the industry have improved efficiency and reliability tremendously. If you want to improve your MPI process then take measures do the following 5 most effective process improvements:
- Highlight indications with LED UV lighting
- Minimize test setup with recipes saved on the machine
- Double inspection speed with a multi-directional machine
- Improve speed and reliability with instant electronic record keeping
- Improve speed and reliability with automation